pump discharge pressure
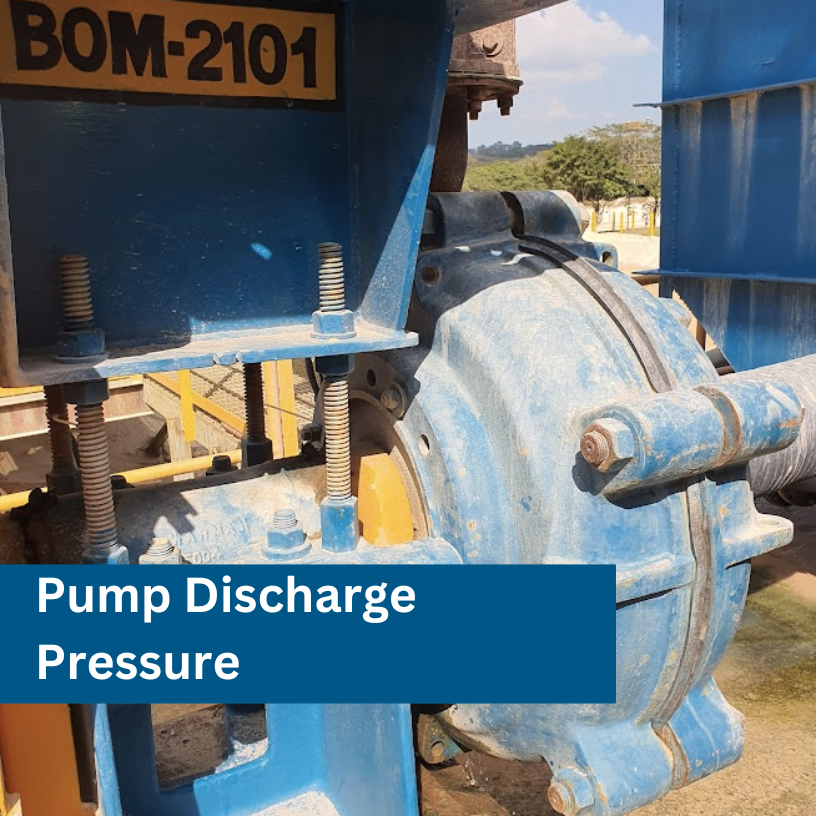
As plant operations personnel, we understand the importance of efficient pump systems. One of the critical components that determines the effectiveness of a pumping system is the pump discharge pressure. The pressure of the fluid being pumped is directly related to the energy required to move it through the system. Therefore, maintaining the optimal pump discharge pressure is crucial for ensuring that the system operates efficiently and effectively. In this article, we will discuss the importance of pump discharge pressure and how it can impact system performance.
What is the typical pump discharge pressure?
As plant operations personnel, you know that pump discharge pressure is a crucial factor in ensuring the efficient and effective operation of your industrial pumping systems. The typical pump discharge pressure can vary widely depending on the specific application and the type of pump being used.
In general, centrifugal pumps commonly used in industrial settings typically have a discharge pressure range of between 30 and 200 psi. Positive displacement pumps, on the other hand, are often capable of generating much higher pressures, ranging from 500 psi up to over 10,000 psi.
It is important to note that pump discharge pressure is not a fixed value but rather a dynamic parameter that can fluctuate depending on a variety of factors, including the flow rate, viscosity of the fluid being pumped, and the system's resistance to flow. As such, it is crucial to monitor and adjust pump discharge pressure regularly to ensure optimal performance and prevent damage to the system.
How is the pump discharge pressure controlled?
As plant operations personnel, you are responsible for ensuring that industrial pumps are functioning correctly and efficiently. One important aspect of pump operation is controlling the discharge pressure. In this blog post, we will explore the various methods that can be used to control pump discharge pressure.
It is crucial to comprehend that a variety of variables, such as pump speed, impeller diameter, and piping system resistance, have an impact on the discharge pressure. The most common method of controlling pump discharge pressure is through the use of a control valve . This valve is installed in the discharge line and is used to restrict the flow of fluid, thereby increasing the pressure.
Control valves can be operated manually or automatically, depending on the system requirements. An operator adjusts manual valves, whereas automatic valves use sensors and other feedback mechanisms to adjust the valve position in response to changes in the system.
Another method of controlling pump discharge pressure is through the use of a variable frequency drive (VFD). A VFD is an electronic device that controls the speed of the pump motor, which in turn controls the pump flow rate and discharge pressure. By adjusting the frequency of the electrical signal that controls the motor, the VFD can increase or decrease the pump speed and thus the pressure.
Finally, it is worth mentioning that some pump systems use a combination of a control valve and a VFD to achieve precise control over the discharge pressure. This approach can provide greater flexibility and control over the system, but it may be more complex and costly to implement.
When it comes to controlling pump discharge pressure, it is important to consider the specific requirements of your system and choose the method that will provide the best results. Regular monitoring and adjustments are also crucial to ensuring that the pump is operating efficiently and preventing any damage to the system.
Is a higher pump discharge pressure more efficient?
When it comes to pump operation, it's easy to assume that a higher discharge pressure is more efficient. However, this is not necessarily the case. In fact, there are several factors to consider when determining the efficiency of a pump system.
Firstly, it's important to understand that pump efficiency is not solely based on discharge pressure but also on flow rate and head. The best way to maximize efficiency is to find the right balance between these three factors.
Additionally, a higher discharge pressure can actually lead to decreased efficiency if it results in excessive energy consumption. This can occur if the pump is operating on the far right side of its performance curve, where the amount of energy required to maintain high pressure far outweighs the benefits.
On the other hand, a lower discharge pressure may be more efficient if it allows the pump to operate closer to its ideal performance range. By reducing the energy required to maintain pressure, the pump can operate more efficiently and effectively.
On Ultimately, the most efficient pump system will depend on the specific application and operating conditions. It is important to work with a knowledgeable pump supplier to determine the best system for your needs and optimize it for maximum efficiency.
What factors affect pump discharge pressure?
As plant operations personnel, it is important to understand the various factors that can affect pump discharge pressure in order to maintain optimal pump performance. Here are some of the key factors to consider:
- Pump speed: The speed at which a pump operates can have a significant impact on its discharge pressure. Generally, higher pump speeds result in higher discharge pressures, while lower speeds result in lower pressures.
- Pump size: The size of the pump also plays a role in determining discharge pressure. Larger pumps are typically capable of producing higher pressures than smaller pumps.
- Pump type: Different types of pumps (e.g., centrifugal, positive displacement) have different pressure capabilities, so it is important to choose the right type of pump for the specific application.
- Fluid properties: The properties of the fluid being pumped can also affect discharge pressure. Factors such as viscosity, density, and temperature can all impact pump performance.
- Pipe diameter and length: The diameter and length of the pipes through which the fluid is being pumped can also affect discharge pressure. Longer or narrower pipes can result in lower pressures, while shorter or wider pipes can result in higher pressures.
- Inlet conditions: The conditions at the pump inlet, such as the presence of air or debris, can also impact discharge pressure. It is important to ensure that the inlet conditions are optimized for maximum pump performance.
By understanding these factors and how they interact with each other, plant operations personnel can take steps to optimize pump performance and ensure that their pumping systems are functioning at their best. This can include regular maintenance and inspection of pumps as well as monitoring of operating conditions to identify any potential issues before they become major problems.
In conclusion, a variety of factors, including pipe diameter, fluid properties, and pump speed and size, affect pump discharge pressure. As plant operations personnel, it's crucial to understand these factors and take steps to optimize pump performance and ensure that your pumping system is functioning at its best. With the help of a knowledgeable pump supplier like Dynapro Pumps, you can achieve optimal pump performance and contribute to a more sustainable industrial future.
- Art
- Causes
- Crafts
- Dance
- Drinks
- Film
- Fitness
- Food
- Games
- Gardening
- Health
- Home
- Literature
- Music
- Networking
- Other
- Party
- Religion
- Shopping
- Sports
- Theater
- Wellness