How EB Welding Is Shaping the Future of Renewable Energy
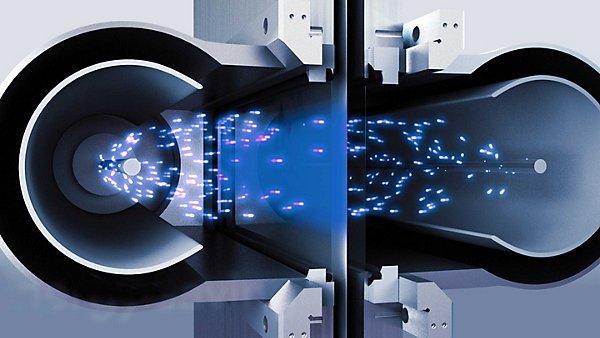
The renewable energy sector is at the forefront of the global push for sustainability, and innovation in manufacturing plays a crucial role in driving its success. Electron Beam (EB) welding is one such innovation, providing precise, efficient, and reliable solutions for creating critical components in renewable energy systems. From wind turbines to solar panels, EB welding ensures high-performance and long-lasting results.
This article explores how EB welding is transforming renewable energy manufacturing, its key applications, and why it is an essential technology for the future of clean energy. For an in-depth guide to EB welding, visit https://ebeammachine.com/electron-beam-welding-the-ultimate-guide-to-high-precision-metal-joining/.
Challenges in Renewable Energy Manufacturing
Producing components for renewable energy systems requires overcoming several challenges:
- Material Durability: Components must withstand harsh environmental conditions like high winds, extreme temperatures, and corrosion.
- High Precision: Wind turbines, solar panels, and other energy systems demand tight tolerances and defect-free welds for optimal performance.
- Efficiency: Manufacturing processes must be efficient to keep costs manageable while scaling up production.
- Sustainability: Minimizing waste and energy consumption during production is vital for aligning with renewable energy goals.
EB welding addresses these challenges with its advanced capabilities and high-performance results.
How EB Welding Benefits Renewable Energy Manufacturing
1. High-Quality Welds for Extreme Durability
Renewable energy components are exposed to harsh conditions, making the quality and strength of welds critical. EB welding creates defect-free joints that ensure durability and reliability.
- Example: Wind turbine blades welded with EB technology maintain their integrity under high stress and constant motion.
2. Precision for Complex Designs
The precision of EB welding allows for the creation of intricate designs and complex geometries. This is essential for optimizing the performance of renewable energy systems.
- Example: In solar panel assembly, EB welding ensures tight connections in thin-film photovoltaic cells, maximizing energy efficiency.
3. Joining Advanced Materials
Many renewable energy components require the use of advanced materials like titanium, stainless steel, and composites. EB welding excels at joining these materials with minimal defects and maximum strength.
- Example: Heat exchangers in geothermal energy systems benefit from EB welding’s ability to join corrosion-resistant alloys.
4. Minimal Material Waste
EB welding’s precise energy application minimizes material waste, reducing costs and supporting sustainability efforts. This is particularly valuable when working with expensive or rare materials.
- Benefit: Lower production costs and a reduced environmental footprint.
5. Energy-Efficient Process
EB welding consumes less energy compared to traditional welding methods by focusing heat precisely on the joint area. This aligns with the renewable energy sector’s goal of reducing overall energy consumption.
- Example: Manufacturing processes for wind turbine components become more sustainable with EB welding.
Applications of EB Welding in Renewable Energy
1. Wind Turbines
Wind turbines rely on large, durable components like blades, nacelles, and towers. EB welding ensures these parts can withstand high stress, fatigue, and environmental conditions.
- Use Case: Blade roots and flanges are welded using EB technology to achieve high-strength, defect-free joints.
2. Solar Panels
The efficiency of solar panels depends on the precise assembly of photovoltaic cells and structural frames. EB welding provides the accuracy and reliability needed for these critical connections.
- Use Case: Thin-film solar panels are welded with EB techniques to maintain optimal energy capture and reduce production defects.
3. Energy Storage Systems
Battery enclosures and other energy storage components require strong, reliable welds to ensure safety and longevity. EB welding meets these demands with precision and consistency.
- Use Case: Lithium-ion battery casings for solar and wind energy storage systems are welded using EB technology.
4. Geothermal Systems
Geothermal plants use heat exchangers and pipelines that must resist corrosion and extreme temperatures. EB welding is ideal for creating strong, durable joints in these systems.
- Use Case: High-performance heat exchangers are manufactured using EB welding to ensure efficiency and longevity.
5. Hydropower
Hydropower systems often involve large, complex components like turbines and gates. EB welding’s ability to produce defect-free, high-strength welds makes it a valuable tool in this sector.
- Use Case: Turbine blades and casings in hydropower plants are welded with EB techniques to ensure durability and efficiency.
Advantages of EB Welding for Renewable Energy
1. Long-Term Reliability
The high-quality welds produced by EB welding enhance the lifespan and performance of renewable energy components, reducing maintenance costs and downtime.
2. Cost-Effectiveness
By minimizing material waste, reducing energy consumption, and streamlining production, EB welding lowers manufacturing costs while maintaining superior quality.
3. Scalability
EB welding systems can be scaled to handle large components, making them ideal for high-volume production in the renewable energy sector.
4. Sustainability
EB welding aligns with the renewable energy industry’s sustainability goals by reducing waste, energy usage, and emissions during production.
Innovations in EB Welding for Renewable Energy
AI-Optimized Welding
Artificial intelligence is being integrated into EB welding systems to optimize parameters and improve efficiency, ensuring consistent quality at lower costs.
Real-Time Monitoring
IoT-enabled sensors provide real-time feedback during welding, allowing for immediate adjustments to ensure defect-free joints.
Advanced Materials Research
New materials compatible with EB welding are being developed, expanding its applications in renewable energy.
Hybrid Welding Techniques
Combining EB welding with other technologies enhances its versatility and efficiency, further benefiting renewable energy manufacturing.
Challenges in Renewable Energy Manufacturing and How EB Welding Overcomes Them
-
High Initial Costs: Manufacturing renewable energy components can be expensive.
- Solution: EB welding reduces waste and energy consumption, lowering overall production costs.
-
Stringent Quality Standards: Renewable energy systems must meet strict performance criteria.
- Solution: EB welding delivers defect-free, durable joints that meet or exceed industry standards.
-
Material Challenges: Advanced materials can be difficult to weld with traditional methods.
- Solution: EB welding excels at joining high-performance materials with precision.
Explore More About EB Welding
To learn more about how EB welding is transforming renewable energy manufacturing, visit https://ebeammachine.com/electron-beam-welding-the-ultimate-guide-to-high-precision-metal-joining/. This guide provides detailed insights into the technology, benefits, and applications of EB welding.
Conclusion
EB welding is playing a vital role in advancing renewable energy by enabling the efficient, reliable, and sustainable production of critical components. Its precision, ability to join advanced materials, and alignment with sustainability goals make it an indispensable technology for the future of clean energy.
As the renewable energy sector continues to grow, EB welding will remain a key enabler of innovation and efficiency. Whether you’re manufacturing wind turbines, solar panels, or energy storage systems, EB welding offers the tools needed to drive progress and create a greener future.
- Art
- Causes
- Crafts
- Dance
- Drinks
- Film
- Fitness
- Food
- Jogos
- Gardening
- Health
- Início
- Literature
- Music
- Networking
- Outro
- Party
- Religion
- Shopping
- Sports
- Theater
- Wellness
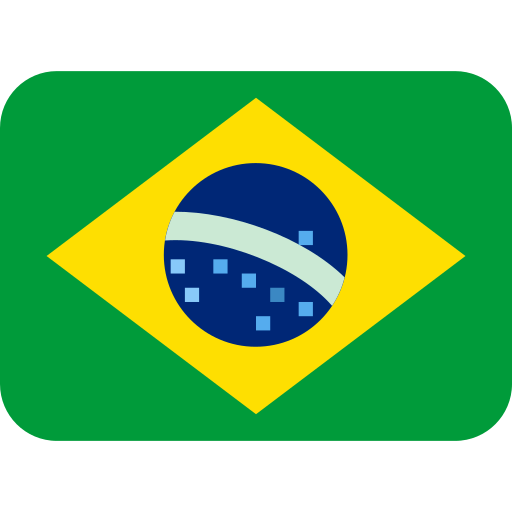