Top Challenges Faced by MEP Estimators and How to Overcome Them
Mechanical, Electrical, and Plumbing (MEP) estimators play a crucial role in the construction and building industries. Their primary responsibility is to estimate the costs of MEP systems and services required for a construction project. These estimations help project managers, contractors, and developers set accurate budgets, plan resources, and meet deadlines. However, the role of an MEP estimator is complex and comes with a range of challenges. In this article, we will discuss the top challenges faced by MEP estimators and explore strategies to overcome them.
1. Inaccurate or Incomplete Project Specifications
One of the primary challenges faced by MEP estimators is dealing with incomplete or inaccurate project specifications. The accuracy of an MEP estimate is highly dependent on the quality of the provided project details. If the project specifications are vague or incomplete, it can lead to erroneous cost calculations, which could result in cost overruns, project delays, or underestimations.
Solution:
To mitigate this issue, MEP estimators must ensure that they thoroughly review project specifications before beginning the estimation process. They should collaborate closely with architects, engineers, and project managers to clarify any ambiguities. In addition, estimators can use their experience and industry knowledge to fill in gaps when complete information is unavailable.
Furthermore, using detailed and up-to-date plans, blueprints, and 3D models can help estimators ensure accuracy. Technology, such as Building Information Modeling (BIM), is becoming increasingly valuable in this regard, as it allows all parties involved in a project to have access to real-time data.
2. Rising Material Costs and Supply Chain Disruptions
Material costs are always fluctuating, and in recent years, global supply chain disruptions have made the situation even more unpredictable. MEP estimators often face the challenge of estimating the cost of materials, which is essential for generating an accurate total project estimate. The volatility in prices of materials such as copper, steel, and other specialized MEP components can significantly affect the final cost.
Solution:
To address this challenge, MEP estimators should stay informed about market trends and be proactive in negotiating with suppliers. Establishing long-term relationships with reliable suppliers can help lock in prices or provide better discounts, making it easier to manage price fluctuations.
Estimators can also use contingency factors to account for potential price increases. Having flexible and adjustable estimates will allow project stakeholders to adapt to changing conditions without compromising the overall project plan.
3. Complexity in Estimating Labor Costs
Labor costs are another significant factor in MEP estimating services. Accurately forecasting labor hours and costs can be challenging due to the variability in the skill levels of workers, regional labor rates, and labor productivity. Additionally, estimating labor costs for specialized tasks, such as installing high-tech HVAC systems or complex electrical wiring, can be particularly tricky.
Solution:
To overcome this challenge, MEP estimators need to rely on historical data, industry standards, and regional labor rate surveys. Estimators can also engage with contractors or subcontractors who have experience in the specific tasks to get a more accurate assessment of labor requirements.
Another approach is to break down the tasks into smaller, manageable components. This allows for more precise estimations for each phase of the work, resulting in a more accurate overall estimate. Moreover, using software tools like project management platforms and estimating software can streamline the process by providing pre-built labor rate databases, helping estimators predict labor costs more accurately.
4. Changes in Project Scope and Design Modifications
Design changes and modifications in the project scope are common during the construction phase, and these changes often affect the MEP systems. Whether the modifications are due to changes in the building layout, additional requirements from clients, or unforeseen obstacles, MEP estimators are often tasked with adjusting the initial estimates to reflect these changes. These adjustments can be time-consuming and complex, especially when they involve substantial alterations to the MEP systems.
Solution:
To deal with scope changes effectively, MEP estimators should build a flexible and adaptable approach into their estimating process. Communication with the project team is key to identifying potential changes early on, allowing estimators to adjust estimates promptly.
It’s also crucial for estimators to maintain a detailed record of any design modifications or scope changes. A solid system for tracking changes can help prevent miscommunication and ensure that revised estimates are accurate. In some cases, estimators can use software that automatically updates cost estimates based on real-time changes in project specifications.
5. Limited Access to Accurate Project Data
Another significant challenge MEP estimators face is the limited access to accurate, up-to-date project data. Estimating is only as good as the information available. If estimators do not have access to the latest project data or if the data is incomplete, it can lead to inaccurate estimates.
Solution:
To overcome this, MEP estimators should implement systems to ensure data is constantly updated and shared across all team members. Using cloud-based platforms or project management software can centralize project data and make it accessible to all stakeholders, ensuring that estimators have the most current information at all times.
Additionally, working closely with other teams, such as architects, engineers, and contractors, can help estimators ensure that they have access to the most accurate and relevant data.
6. Technological and Software Challenges
The integration of technology in the construction industry is increasing rapidly, and MEP estimators are often required to use specialized software for creating detailed estimates. However, the fast-paced evolution of software tools can create a learning curve for many estimators, especially those who may not be tech-savvy. Additionally, software tools can be expensive and require proper training to maximize their potential.
Solution:
To overcome technological challenges, MEP estimators should invest in training and familiarize themselves with the latest estimation software tools available in the market. There are many comprehensive software solutions designed specifically for MEP estimators that can help automate calculations and generate more accurate estimates. A good understanding of these tools can increase efficiency and reduce human errors.
Additionally, estimators should collaborate with the IT department to ensure that the software tools are seamlessly integrated into the overall project management ecosystem. This helps to streamline workflows and reduce the time spent on manual calculations.
7. Difficulty in Coordinating with Other Trades
Construction projects often involve multiple trades working simultaneously, and MEP systems have to be coordinated with other aspects of the project, such as structural, architectural, and civil elements. Any lack of coordination or miscommunication between different trades can result in costly delays, rework, or design errors, which directly impact MEP estimation accuracy.
Solution:
Effective communication and collaboration are essential to avoid coordination issues. MEP estimators should regularly meet with other teams, such as civil engineers, architects, and contractors, to discuss any potential issues and make necessary adjustments to the project. Using tools like BIM can also help ensure that all team members have a unified view of the project, minimizing conflicts between trades.
8. Legal and Regulatory Compliance
The construction industry is heavily regulated, and MEP systems must comply with various legal and regulatory standards, including safety codes, environmental regulations, and energy efficiency requirements. Failing to account for these regulations during the estimating process can lead to costly penalties or redesigns.
Solution:
MEP estimators need to stay updated on local building codes, regulations, and industry standards. They should work closely with legal advisors and regulatory bodies to ensure that all estimates account for these compliance requirements. Utilizing software that is tailored to local regulations can also help ensure that estimates are always in line with the latest legal standards.
Conclusion
While MEP estimating comes with a set of significant challenges, the right strategies and tools can help estimators overcome them. From improving communication and staying updated on market trends to leveraging advanced software tools, MEP estimators can enhance their ability to deliver accurate and reliable cost estimates. By focusing on precision, adaptability, and collaboration, MEP estimators can ensure successful project outcomes and contribute to the efficiency and profitability of the construction industry.
- Art
- Causes
- Crafts
- Dance
- Drinks
- Film
- Fitness
- Food
- Jogos
- Gardening
- Health
- Início
- Literature
- Music
- Networking
- Outro
- Party
- Religion
- Shopping
- Sports
- Theater
- Wellness
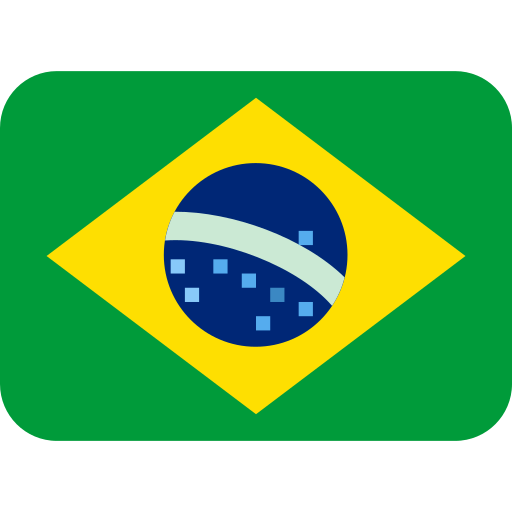