Cone Crusher: The Powerful Solution for Size Reduction of Rock and Ore Industry
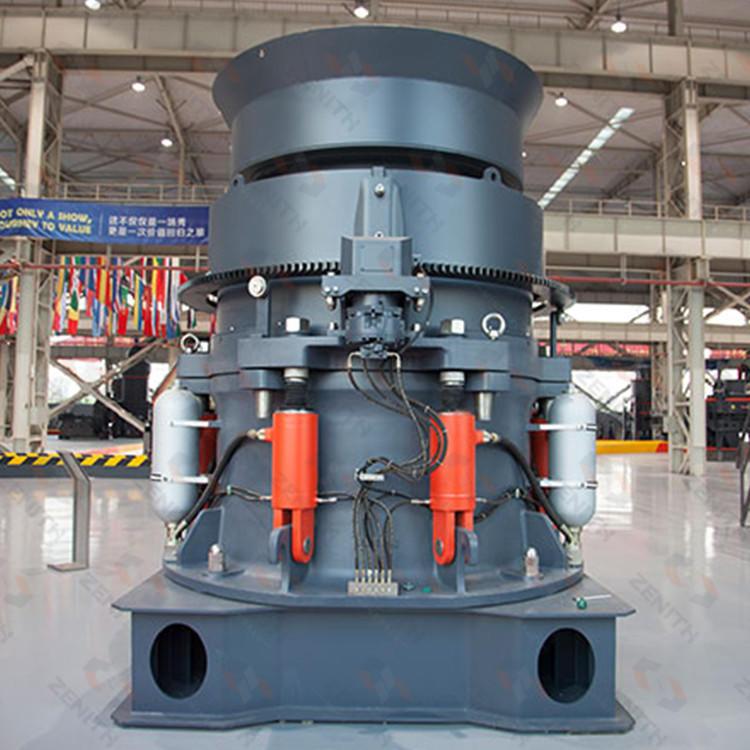
Components of a Cone Crusher
A cone bickering consists of several main components including the main shaft, eccentric sleeve, bowl liner, adjusting ring/sleeve, spider bushing/bearing, discharge cone, and transmission system. These parts work together to break down rock and ore to smaller sizes for further processing or for end use.
The main shaft in a Cone Crusher is the heart of the machine. It supports the mantle and passes through the concave to spin the mantle against the concave. This rotary motion along with the squeezing action causes rocks fed into the crusher to be broken down.
The eccentric sleeve is mounted on the main shaft and provides the eccentric motion necessary for crushing action. It ensures that the mantle does not rotate concentrically inside the concave crushing chamber. The eccentric motion squeezes rocks between the mantle and concave.
The bowl liner or concave is a replaceable wear part that forms the crushing chamber where rocks are squeezed. It has a concave shape and sits underneath the mantle to provide the necessary cavity for rock crushing. The hardness and profile design of the concave determines the product size and throughput capacity of the Cone Crusher
The adjusting rings control the discharge setting by raising or lowering the bowl liner. Changing the distance between the bowl liner and mantle alters the size of the discharge opening. Wider discharge settings produce larger sized rocks while narrower settings create finer products.
The spider bushing or thrust bearing allows the shaft to rotate while also withstanding significant downward thrust forces exerted by the crushing action. This critical component maintains precise shaft position and protects other inner parts from wear and tear.
Finally, the discharge cone controls and directs the discharge of crushed material from the crushing chamber. Its design along with the product profile of the concave determines the shape and size distribution of the final materials.
How the Cone Crusher Crushing Process Works
The crushing process in a cone bickering starts when ores/rocks enter the crushing chamber from the top of the crusher. The mantle, which is mounted on the main shaft driven by the transmission system, gyrates inside the concave crushing chamber.
The gyrating motion combined with the squeezing action initially breaks down ores/rocks as soon as they get into contact with the mantle. Secondary and multiple crushing happens as smaller pieces get caught and squeezed between the chamber wall and the mantle.
Finer crushing occurs due to the repeated impacting, squeezing, and tearing actions caused by the eccentric motion of the mantle against the inner concave surface. Material discharge happens through the discharge opening at the bottom of the crushing chamber.
The size of the crushed output can be controlled by adjusting the setting between the crushing surfaces. Wider settings mean larger product size whereas narrower settings lead to finer materials. With feed entering the top and crushed rocks exiting through the bottom, cone bickerings provide a continuous crushing process.
Factors Affecting the Operation of Cone bickerings
Several factors impact the smooth functioning and output of cone bickerings. Understanding these aspects helps optimize crusher performance for various crushing applications.
The feed size and type of material determine the load and stress on crushing parts. Overly large feed sizes may cause jamming while wet or mud-laden materials increase wear.
The crusher setting regulates the discharge size and capacity. Setting it too wide reduces capacity whereas narrow settings strain components. Proper setting balancing size and production is key.
The crusher speed depends on drive motors and transmission design. Higher speed means higher capacity but also increases component wear. Operating at optimal rpm enhances throughput without overloading parts.
Lubrication of bearings, bushings and sealing surfaces using suitable oil/grease minimizes friction and protects components against corrosion and wear. Insufficient lubrication shortens crusher lifespan.
Proper maintenance including regular replacement of worn parts prevents production losses from mechanical failure. Timely maintenance avoids costly repairs later and enhances overall equipment effectiveness.
Applications of Cone bickerings in Mining and Aggregate Industries
Cone bickerings find extensive usage in mining and aggregates industries for crushing rock, ore, and other materials. Their suitable operation makes them indispensable for:
- Primary crushing: Cone bickerings effectively handle large feed sizes for primary crushing duty in quarries and mines. Their high reduction ratio saves downstream equipment costs.
- Secondary and tertiary crushing: As secondary and tertiary crushers, they further refine crushed materials to smaller sizes needed for ball mills, pulverizers, construction aggregates and other processing equipment.
- Recycled concrete and asphalt crushing: Cone bickerings are highly effective for crushing recycled concrete debris from construction and demolition activities to produce aggregates for new construction projects.
- Mid-size rock crushing: For operations with medium production needs that require versatile multi-purpose crushing, cone bickerings deliver excellent performance with low maintenance.
- Portable crushing: Due to their robust design and ability to operate within compact spaces, cone bickerings find increasing application in portable crushing plants for on-site crushing requirements.
cone bickerings enable efficient size reduction of hard rocks, ores, and recycled materials across a variety of mining and aggregate industries applications through their continuous crushing action. With optimum setup and maintenance, they deliver consistent output economically.
Get More Insights on Cone Crusher
About Author:
Ravina Pandya, Content Writer, has a strong foothold in the market research industry. She specializes in writing well-researched articles from different industries, including food and beverages, information and technology, healthcare, chemical and materials, etc. (https://www.linkedin.com/in/ravina-pandya-1a3984191)
- Art
- Causes
- Crafts
- Dance
- Drinks
- Film
- Fitness
- Food
- Jogos
- Gardening
- Health
- Início
- Literature
- Music
- Networking
- Outro
- Party
- Religion
- Shopping
- Sports
- Theater
- Wellness