Electronic Chemicals: Enablers of Modern Technology
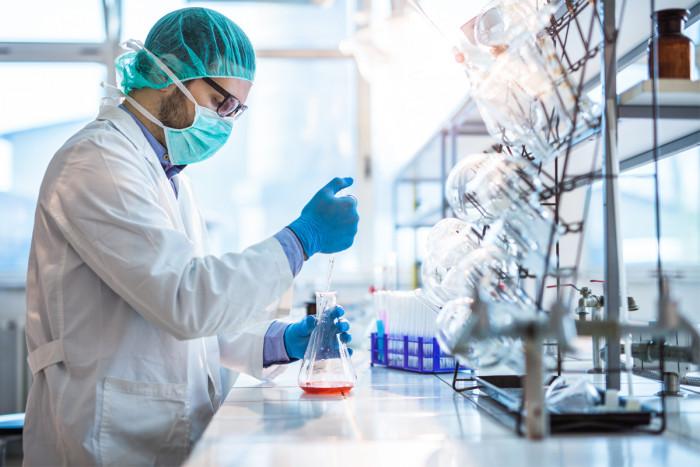
Electronic chemicals play a crucial role in the manufacturing of various electronic devices and components that we use in our daily lives. These chemicals are involved right from the basic circuit board manufacturing to the advanced semiconductor fabrication processes. Some of the key chemicals include photoresists, liftoff resists, etchants, CMP slurries, cleansing agents and various specialty chemicals. Let us deep dive into various types and applications of these electronic chemicals.
Photoresists - Foundation for precise circuit patterns
Electronic Chemicals are light-sensitive resins that are core to the semiconductor fabrication process. During circuit board manufacturing or IC fabrication, a thin layer of photoresist is applied on the substrate. This layer is then exposed to ultraviolet light through a photo-mask. The light activates the chemical changes in the exposed areas of photoresist. Depending on the type, the exposed or unexposed areas either become soluble or insoluble in the developer solution. The developer then washes away the soluble areas, leaving behind the circuit pattern on the substrate. This ability of photoresists to precisely transfer circuit patterns through photolithography makes them one of the most important electronic chemicals. Major types of photoresists used are positive and negative tone resists.
Liftoff resists - Enabling metallization and diverse applications
Liftoff resists find wide application for selective metal deposition in manufacturing printed circuit boards, hybrid circuits, MEMS devices, sensors and various other micro-devices. In the liftoff process, a layer of liftoff resist is patterned over the substrate, just like a photoresist, using a developer. Then, metal such as copper, gold or aluminum is evaporated over the entire surface. Due to the insulating property of liftoff resist, the metal adheres only to the exposed areas of the substrate. The resist along with the metal overburden is then dissolved, leaving back the desired metal pattern. This unique ability of liftoff resists to selectively attach and remove metal films through a simple wet stripping process simplifies metallization steps for many electronic components.
Etchants - Sculpting circuits layer by layer
Etchants play a vital role in sculpting thin film layers during multilayer circuit manufacturing and semiconductor processing. These are chemical formulations that selectively remove materials by an etching process. In dry etching, gases like chlorine or fluorine based chemistry is used to anisotropically etch materials like silicon, oxide and nitride. Whereas, wet etching involves the use of liquid chemical solutions to selectively dissolve away exposed thin film materials like metal or dielectric layers. Isotropic wet etchants for silicon include TMAH and KOH solutions. Plasma ashers use oxidative plasma to selectively remove organic residues. Precise control over etch rates and selectivity is important to obtain well-defined circuit patterns and cross-sections.
CMP slurries - Enabling planar surfaces for advanced nodes
Chemical mechanical planarization or CMP has become an indispensable process for global planarization in current semiconductor manufacturing. CMP slurries contain abrasive particles like silica or alumina along with chemical oxidizing or chelating agents. During CMP, the slurry is used as a medium between the substrate and a polishing pad. The mechanical abrasion by the particles along with the chemical dissolution or passivation of surface films allows globally planarizing thick metal stacks, interlayer dielectrics and other thin films. Advanced CMP slurries capable of planarizing at finer nodes with less defects are continually researched and developed. Leading manufacturers offer slurries tailored for different materials like tungsten, copper, Low-k dielectrics and barrier layers.
Cleansing Agents - Keeping processing pristine
Ultra-high purity cleansing agents play a key role in maintaining pristine cleanroom environments needed for critical semiconductor fabrication. These include solvents, acids and alkaline cleaners used at various stages for cleaning wafer surfaces, process chambers, tool parts and apparel. Semi-aqueous and aqueous formulations support safer handling compared to hazardous solvents. Effective rinsing is equally important to remove trace impurities left by the cleansers. Advances in formulations with low particle and metal contamination levels allow addressing stringent cleanliness requirements. Leading suppliers offer customized systems and programs for cleansing applications at various technology nodes.
Specialty electronic chemicals
Apart from the above categories, there are host of other specialty electronic chemicals finding diverse niche applications. Anti-reflective coatings (ARCs) are used to suppress reflection during photolithography for better resolution. Spin-on dielectrics provide alternatives to PECVD oxides for improved gap-fill. Metal organic precursors enableDeposition of films like tungsten, cobalt and titanium through MOCVD and ALD. Diffusion inhibitors and getters scavenge mobile ions to prevent degradation. Hydrofluoric acid (HF) etchesnative oxide and cleaning residue on various surfaces.All these chemicals precisely engineered at molecular level have made miniaturization of electronic components possible into the deep sub-micron range.
Environmental and sustainability aspects
With the growing complexity of electronic devices, the demand as well as environmental impact of electronic chemicals is increasing rapidly. Many traditional wet process chemistries involve hazardous acids, bases, solvents and heavy metals. Strict regulations are in place around their production, transportation, usage and disposal in developed nations. However, recycling and reusing of expensive precious metal slurries remains a challenge. Alternative more sustainable approaches being explored include dry plasma based processes, usage of aqueous formulations and green photolithography solutions. Chemical manufacturers are also intensifying R&D efforts towards green syntheses, on-toxic alternatives and reducing waste generation. Collective efforts between industry, academia and authorities will be key to progress semicon manufacturing onto a greener, circular path.
electronic chemicals form the very backbone of modern electronics manufacturing industry. Right from the initial circuit design to the final packaging and testing stages, these specially engineered chemicals precisely enable diverse microfabrication steps. Continuous innovation in chemical material formulations tailored for newer devices at advanced technology nodes will remain crucial. At the same time,adoptinggreener and more sustainable approaches is equally important from environmental standpoint. With increasing miniaturization needs, it seem poised for further growth along with responsibly addressing ecological challenges.
Get More Insights on- Electronic Chemicals
About Author:
Ravina Pandya, Content Writer, has a strong foothold in the market research industry. She specializes in writing well-researched articles from different industries, including food and beverages, information and technology, healthcare, chemical and materials, etc. (https://www.linkedin.com/in/ravina-pandya-1a3984191)
- Art
- Causes
- Crafts
- Dance
- Drinks
- Film
- Fitness
- Food
- Jeux
- Gardening
- Health
- Domicile
- Literature
- Music
- Networking
- Autre
- Party
- Religion
- Shopping
- Sports
- Theater
- Wellness