Corrosion Protective Coatings: A Necessary Barrier for Steel Structures
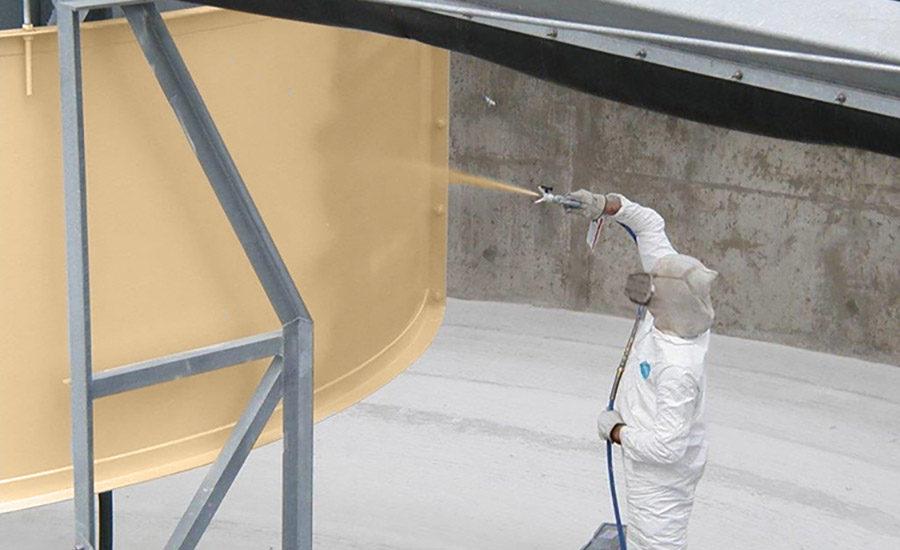
Corrosion is a natural process that converts refined metals to a more chemically-stable form such as rust. It is the gradual destruction of materials (usually metals) by chemical and electrochemical reaction with their environment. For structures like ships, bridges and industrial equipment, corrosion can significantly compromise integrity and structural performance if left unchecked. It is estimated that corrosion costs developed economies hundreds of billions of dollars each year in maintenance, repair and replacement.
Types of Corrosion Protective Coatings
There are several types of Corrosion Protective Coatings utilized for steel structures depending on the environmental conditions and required performance.
Paint Coatings
Paint coatings are the most commonly used corrosion protective system. They provide an effective barrier against corrosion by separating the steel substrate from the surrounding environment. Various paint coatings include enamel paints, epoxy paints, polyurethane paints and vinyl-based paints. Epoxy paints have excellent adhesion and can tolerate higher temperatures compared to other paints. They are often used in harsh, highly corrosive conditions.
Galvanizing
Galvanizing involves applying a zinc coating to steel for cathodic protection. Zinc provides sacrificial protection to the underlying steel - if the zinc corrodes, the steel is protected. Hot-dip galvanizing is widely used where high corrosion resistance is required. It forms a rugged, corrosion-resistant zinc/iron alloy bond with steel. Mechanically galvanized coatings provide less corrosion protection compared to hot-dipped but are cheaper to apply.
Metallizing
Metallizing uses thermal spraying to apply a thick metallic coating like zinc, aluminum or their alloys to steel surfaces. This is often used in highly corrosive environments like offshore oil rigs. The high-density coating provides excellent barrier protection and cathodic protection. Advanced metallizing technologies allow uniform coatings to be applied to complex steel shapes.
Polymer Coatings
Advanced polymer coating systems provide lighter, more durable barrier protection compared to traditional paints. Polyurea and polyurethane coatings have very high chemical resistance and flexibility. They are increasingly used in infrastructurelike bridge deck waterproofing membranes. Epoxy coating systems are preferred where resilience to weathering and chemical spills is required.
Application and Performance Considerations
Proper surface preparation is critical for coatings to adhere strongly and achieve their designed service life. A minimum Sa 2 near-white metal blast standard is generally required. Edges, corners and gaps must be sufficiently coat to prevent corrosion initiation points. Coatings are often applied in multiple layers - a primer followed by one or more finish coats.
Coatings are selected based on anticipated environmental conditions and required service life. Marine environments are highly corrosive and typically require galvanizing, metallizing or high-performance barrier polymer coatings. Industrial settings may utilize inorganic zinc or epoxy coatings. Infrastructure exposed to de-icing salts demands highly corrosion resistant polymer systems. Proper material selection and quality application ensure protective coatings reinforce steel structures for decades of maintenance-free service.
Inspection and Maintenance
Even with durable coating systems, corrosion protection requires ongoing inspection and maintenance. Coatings degrade over time through weathering, abrasion, or damage. Bare steel exposure leads to rapid corrosion. Routine visual inspections check for coating defects, degradation or underfilm corrosion. Thermographic, ultrasonic or other non-destructive testing methods also effectively detect hidden corrosion.
Any areas where the coating has deteriorated exposing steel must be re-coated before corrosion develops. For marine coatings, occasional cleaning may be needed to remove marine growth if left unchecked. A coating maintenance program that re-applies topcoats before the previous layer wears through can extend the service life indefinitely. With proper selection and upkeep of corrosion protective coatings, steel infrastructure remains strong and durable for generations of service.
Corrosion inflicts extensive economic damage and poses safety issues if left unaddressed. Durable barrier coatings are a critical line of defense for steel structures against corrosion damage. From small industrial parts to massive offshore platforms, coating systems are engineered to provide years of protection in even the harshest environments. With a full understanding of corrosion mechanisms and coatings technology, infrastructure owners can specify systems ensuring steel assets remain sound for their designed service life through natural barrier protection.
Get more insights on – Corrosion Protective Coatings
About Author:
Alice Mutum is a seasoned senior content editor at Coherent Market Insights, leveraging extensive expertise gained from her previous role as a content writer. With seven years in content development, Alice masterfully employs SEO best practices and cutting-edge digital marketing strategies to craft high-ranking, impactful content. As an editor, she meticulously ensures flawless grammar and punctuation, precise data accuracy, and perfect alignment with audience needs in every research report. Alice's dedication to excellence and her strategic approach to content make her an invaluable asset in the world of market insights.
(LinkedIn: www.linkedin.com/in/alice-mutum-3b247b137 )
- Art
- Causes
- Crafts
- Dance
- Drinks
- Film
- Fitness
- Food
- Oyunlar
- Gardening
- Health
- Home
- Literature
- Music
- Networking
- Other
- Party
- Religion
- Shopping
- Sports
- Theater
- Wellness