Top Methods for Reducing and Correcting Weld Undercutting in Your Projects
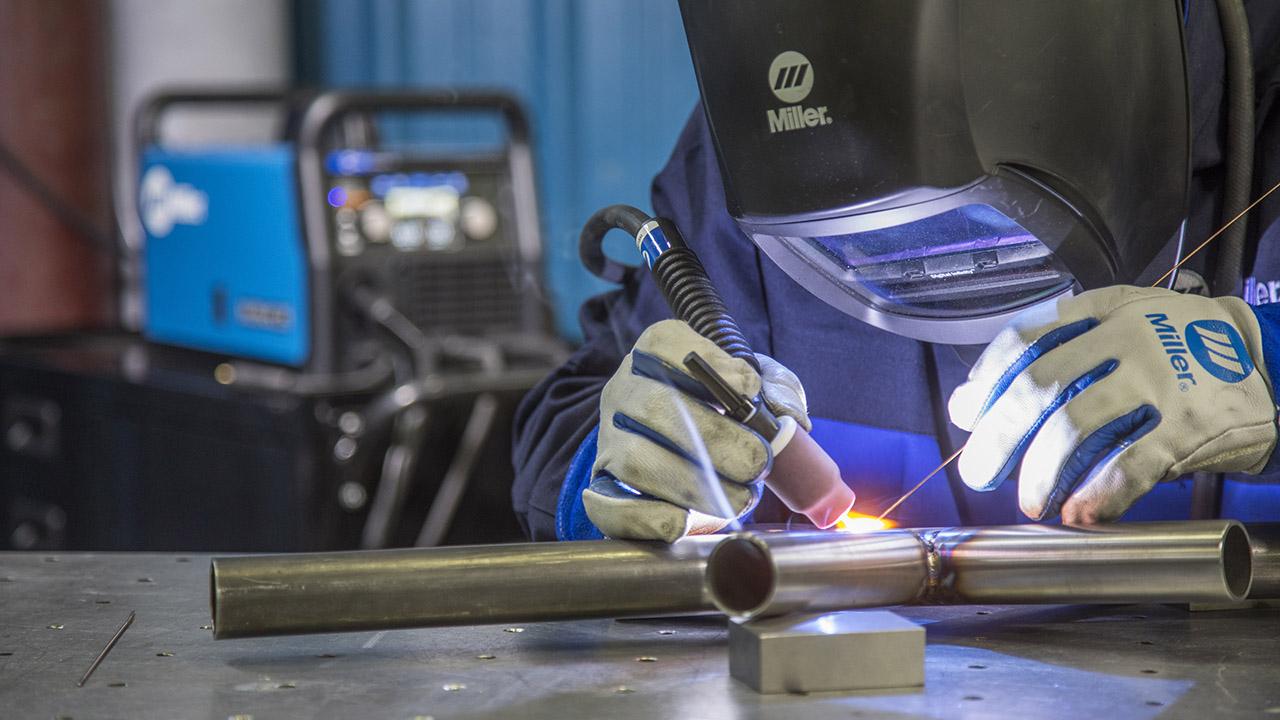
Welding is an essential skill in many industries, but it’s not without its challenges. One of the more common issues welders face is weld undercutting. If you've ever looked at a weld and seen unsightly grooves or recesses, you’ve encountered undercutting. This problem can affect the strength and integrity of your welds, leading to costly repairs and potential failures. In this blog post, we'll dive deep into the top methods for reducing and correcting weld undercutting. Whether you're a seasoned welder or just starting out, this guide will provide practical tips and techniques to help you achieve flawless welds.
Before we get into solutions, let's clarify what weld undercutting is. Weld undercutting occurs when the base metal adjacent to the weld bead erodes or melts away, creating a groove or recess. This defect reduces the strength of the weld and can lead to long-term issues if not properly addressed.
Think of weld undercutting as a poorly done patch on a wall. Instead of a smooth, seamless finish, you end up with gaps and uneven areas that can compromise the overall stability of the structure.
Common Causes of Weld Undercutting
Understanding the causes of weld undercutting is crucial for both prevention and correction. Here are some of the primary culprits:
-
Incorrect Welding Parameters: Using the wrong voltage or amperage settings can lead to excessive heat, causing the base metal to melt away.
-
Improper Technique: Holding the welding torch at an incorrect angle or moving too quickly can create undercuts.
-
Contaminated Base Metal: Rust, paint, or other contaminants on the metal surface can lead to weld defects.
-
Inappropriate Filler Material: Using the wrong filler material or electrode can also contribute to undercutting.
Identifying Weld Undercutting
To address weld undercutting effectively, you first need to identify it. Here’s how you can spot and assess undercutting:
-
Visual Inspection: Look for grooves or recesses along the weld bead. These are often visible to the naked eye.
-
Surface Profile Measurement: Use gauges to measure the depth of any recesses. This will help determine the severity of the defect.
-
Non-Destructive Testing: Techniques like ultrasonic testing or radiography can detect undercuts that might not be visible on the surface.
Methods for Reducing and Correcting Weld Undercutting
Reducing and correcting weld undercutting involves a mix of prevention techniques and repair methods. Here’s a detailed look at some of the best practices:
1. Adjust Welding Parameters
One of the first steps to preventing weld undercutting is to ensure your welding parameters are correctly set. Here’s what to focus on:
-
Voltage and Amperage: Make sure your settings are appropriate for the material you’re welding. Too high or too low can cause problems.
-
Heat Control: Keep the heat level under control to avoid melting the base metal excessively.
2. Improve Welding Technique
Your technique plays a significant role in avoiding weld undercutting. Here’s how to refine it:
-
Maintain Proper Angle: Hold the welding torch at the correct angle to ensure an even weld pool.
-
Control Speed: Move at a steady pace to prevent overheating and undercutting.
-
Practice Regularly: Regular practice helps improve your technique and reduce errors.
3. Clean the Base Metal Thoroughly
Before you start welding, ensure the base metal is clean and free from contaminants:
-
Remove Rust and Paint: Use a wire brush, grinder, or chemical cleaner to prepare the metal surface.
-
Check for Debris: Ensure there’s no dirt or oil on the welding surface.
4. Use the Right Filler Material
Selecting the appropriate filler material and electrode is essential for preventing weld undercutting:
-
Match Materials: Use filler materials that are compatible with the base metal.
-
Check Specifications: Follow manufacturer guidelines for filler material and electrode use.
5. Implement Regular Weld Inspection
Regular inspection helps catch issues early and ensures weld quality:
-
Visual Inspections: Regularly check welds for visible defects.
-
Use Inspection Tools: Employ gauges and non-destructive testing techniques to assess weld quality.
6. Apply Weld Undercut Repair Techniques
If you encounter weld undercutting, there are several effective repair methods:
-
Grind Down the Undercut: Use a grinder to smooth out the undercut and prepare the area for re-welding.
-
Re-Weld the Area: Apply a new weld bead over the prepared surface, ensuring correct technique and parameters.
-
Use Fillers if Necessary: For minor undercuts, filler materials can help correct the defect.
7. Minimize Heat Input
Managing heat input can help prevent weld undercutting:
-
Control Heat Levels: Use just enough heat to create a good weld without excessive melting.
-
Monitor Welding Time: Avoid overheating by limiting the time the torch is applied to any one area.
Conclusion
Weld undercutting can be a frustrating challenge, but with the right knowledge and techniques, you can effectively reduce and correct it. By understanding the causes, implementing prevention strategies, and applying proper repair methods, you can ensure your welds are strong, reliable, and defect-free.
- Art
- Causes
- Crafts
- Dance
- Drinks
- Film
- Fitness
- Food
- Spellen
- Gardening
- Health
- Home
- Literature
- Music
- Networking
- Other
- Party
- Religion
- Shopping
- Sports
- Theater
- Wellness
