Key Trends and Developments in the Global Market for Pharmaceutical Intermediates
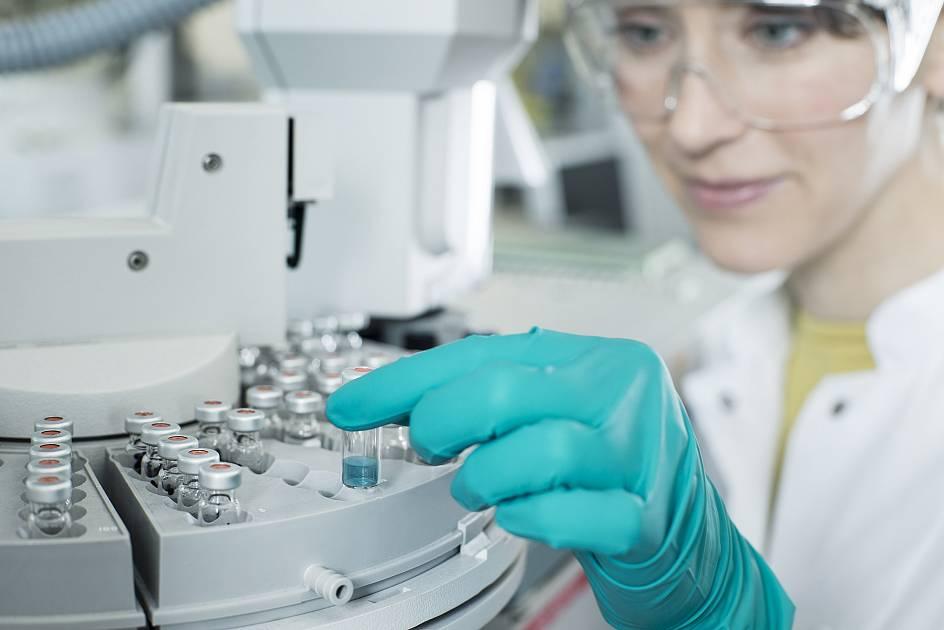
Product Patents and Globalization of Manufacturing:
Over the past two decades, there has been a significant change in the pharmaceutical industry with product patents being granted across different countries. Prior to this, many large drug manufacturers were producing generics of patented drugs in different markets. However, with global harmonization of intellectual property laws driven by the WTO's TRIPS agreement, manufacturers can no longer rely on the generic market in different regions. As a result, they have shifted focus to producing patented drugs as well as the active pharmaceutical ingredients and intermediates required for these molecules. This has led to the globalization of manufacturing for such intermediates. Many Indian and Chinese drug companies now cater to global demand for these products rather than limiting their market within Asia or certain regulated markets.
Outsourcing Of Intermediate Manufacturing:
The patent cliff faced by many "blockbuster" drugs produced by large pharmaceutical companies also drove changes in the industry. When drug patents expired, these firms lost significant sales revenues overnight. To diversify product offerings and reduce risk of future financial losses, they strategically exited non-core intermediate manufacturing and outsourced such activities to dedicated contract manufacturing organizations (CMOs). This allowed pharmaceutical giants to focus on drug development and sales while leveraging specialized global manufacturers for supply of intermediates. Regulatory obligations related to environment, health and safety also encourage outsourcing of chemical production to reliable partners.
Adoption Of Continuous Processing Technologies:
Traditionally, pharmaceutical manufacturing relied heavily on batch processing for production of intermediates and active ingredients. However, the past decade witnessed growing adoption of continuous flow technologies that can improve yields, reduce waste and allow for better control and intensification of chemical processes. Many manufacturers have made capital investments in continuous equipment to gain efficiencies in intermediate production. This has led to better control of quality as well as scaling up of manufacturing capacity compared to conventional batch reactors. Continuous processes may also ease the regulatory burden for certain intermediates being manufactured across international borders.
Shift Towards Single-Use Systems:
Following the trend in biopharmaceutical development and manufacturing, single-use technologies are also being evaluated and commercialized for production of organic Global Pharmaceutical Intermediates and other small molecule APIs. Factors like eliminations of clean-in-place (CIP) procedures, reduction in cross-contamination risks and facilities for smaller batch productions are driving interest in flexible single-use equipment. Although traditional stainless-steel systems remain mainstream, certain manufacturers have demonstrated the technical and commercial feasibility of single-use options for select chemical syntheses. This may feature more prominently for custom synthesis of difficult to manufacture molecules.
Consolidation Among Contract Manufacturers:
With rising costs of manufacturing, complying with regulations as well as demand for reliability of supply chain, large pharmaceutical companies have increasingly preferred to outsource manufacturing to an elite group of global CMOs with comprehensive service offerings across development and commercial supply. This has led to a phase of mergers and acquisitions with mid-sized CMOs being acquired by international leaders across North America, Europe and Asia. The capabilities of larger CMOs to handle multi-product portfolios in different geographies makes them preferred outsourcing partners. Smaller pharmaceutical firms also increasingly rely on such CMOs for manufacture of their intermediates and APIs.
Demand And Regional Production Bases:
Asia, with its affordable manufacturing capabilities has emerged as a major supplier for pharmaceutical intermediates to both regulated and generic drug markets globally. China and India are dominant suppliers accounting for over 60% of global trade volumes. However, geographic diversification of supply sources is an important consideration, especially with rising trade protectionism. As a result, alternatives like manufacturing sites in Europe and North America are gaining prominence to ensure supply security. There is also renewed interest in domestic production within large markets like the US and Japan through collaborations involving government agencies and pharmaceutical majors. New technological solutions making manufacturing competitive will support further regionalization and decentralization of essential intermediate supplies.
Get more insights on – Global Pharmaceutical Intermediates
About Author:
Money Singh is a seasoned content writer with over four years of experience in the market research sector. Her expertise spans various industries, including food and beverages, biotechnology, chemical and materials, defense and aerospace, consumer goods, etc. (https://www.linkedin.com/in/money-singh-590844163)
- Art
- Causes
- Crafts
- Dance
- Drinks
- Film
- Fitness
- Food
- Giochi
- Gardening
- Health
- Home
- Literature
- Music
- Networking
- Altre informazioni
- Party
- Religion
- Shopping
- Sports
- Theater
- Wellness