Phenolic Resins: Processes, Properties and Applications
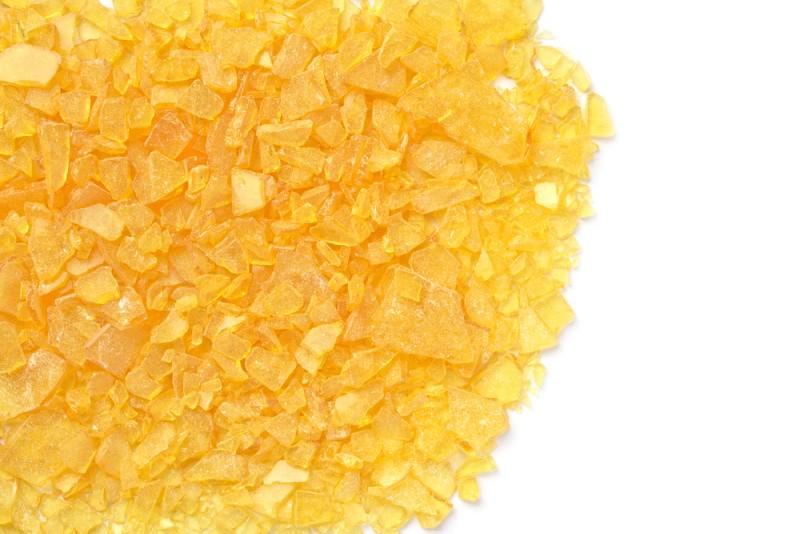
Phenolic resins, also known as phenol-formaldehyde resins, are synthetic polymers that are produced from the reaction of phenol or substituted phenol with formaldehyde. They were first synthesized in the late 19th century and remain widely used in industrial applications today.
Material and Chemical Composition
Phenolic resins are formed via a condensation reaction between phenol and formaldehyde in stoichiometric ratios. The most common formulation is a 1:1 molar ratio reaction of phenol and formaldehyde, which produces a thermosetting resin. Variations in the ratios and addition of other chemicals like cresols allow control over the properties and reactivity of the final resin product. The chemical structures include aromatic hydrocarbons joined by methylene bridges (-CH2-). Common substitutions on the phenol rings include alkyl groups on the ortho or para positions.
Production Processes
Industrially, Phenolic Resins are produced through either one-stage or two-stage polymerization reactions. In the one-stage process, phenol and formaldehyde are added together and polymerized in the presence of an alkaline catalyst like sodium hydroxide. This leads to a rapid mass polymerization. In the two-stage process, the reactants are added sequentially with an initial acid-catalyzed reaction followed by an alkaline-catalyzed one. This allows better control over the polymerization and yields a more uniform molecular weight distribution. Both batch and continuous production methods are employed depending on scale and end-use requirements.
Curing and Properties
As thermosetting polymers, phenol-formaldehyde resins undergo curing or hardening when heated. This involves further polymerization and crosslinking reactions between the reactive sites. The final cured resin exhibits high thermal stability, compression strength, adhesion properties and electrical insulation. The degree of crosslinking and resultant properties can be tailored by adjusting curing conditions like temperature and time. Phenolic resins also have good resistance to acids, alkalis and organic solvents along with reasonable fire retardant properties.
Applications of Phenolic Resins
Given their versatility and balance of properties, phenol-formaldehyde resins find extensive use in areas such as wood adhesives, molding compounds, insulation, refractories, abrasives and friction materials.
As adhesives, they are widely used in plywood, particleboard, oriented strand board (OSB) and fiberboard manufacture due to their high strength and water resistance.
In molding applications, phenol-formaldehyde resins are made into prepregs, short fibers or powders for compression and injection molding of electrical insulators, automobile brake pads, bearings and mechanical parts. They offer heat stability, strength and excellent electrical properties for these uses.
Phenolic resins also serve as excellent electrical insulators due to their resistance to tracking (carbonization on high voltage exposure) and charring. They are therefore used to produce laminates, varnishes and cast resins for both low and high voltage applications.
Phenol-formaldehyde resins have good fire resistance which makes them suitable for applications like thermal and electrical insulators in buildings, aircrafts, ships etc. This property also allows their use in brake linings, foundry cores and refractory/abrasive mixtures.
Friction materials for brakes and clutches utilize phenol-formaldehyde resins for their heat dissipation and wear resistance. Their high mechanical strength and thermal stability ensure long performance life under harsh conditions.
Other smaller niche uses include filters, paper and paper pulp treatment, fabric finishes, etc. Phenolic resins have thus demonstrated sustained industrial significance for nearly a century.
Recent Advances and Future Outlook
Recent research has focused on developing higher performance phenol-formaldehyde resins by modifying synthesis routes and incorporating additives/nanofillers. Some key trends include:
- Use of curing accelerators and alterative catalysts for faster production cycles.
- Development of resoles, novolacs and other specialty phenol-formaldehyde resins for electrical/electronic applications.
- Utilization of bio-based phenols like lignin for more sustainable resins.
- Introduction of nanotubes, boron nitride or silicone additives to further boost thermal, mechanical and flame retardant properties.
- Synthesis of copolymers and blends with other polymers to optimize various properties as per application.
Phenolic resins still dominate many markets due to their favorable balance of properties and economics. With continued advancements, they are projected to retain relevance in major applications over the coming decades. Overall, phenol-formaldehyde resins have firmly established themselves as an indispensable class of industrial polymers.
Get more insights on Phenolic Resins
About Author:
Ravina Pandya, Content Writer, has a strong foothold in the market research industry. She specializes in writing well-researched articles from different industries, including food and beverages, information and technology, healthcare, chemical and materials, etc. (https://www.linkedin.com/in/ravina-pandya-1a3984191)
- Art
- Causes
- Crafts
- Dance
- Drinks
- Film
- Fitness
- Food
- Spellen
- Gardening
- Health
- Home
- Literature
- Music
- Networking
- Other
- Party
- Religion
- Shopping
- Sports
- Theater
- Wellness
