Flare Gas Recovery Systems: Recovering Wasted Flare Gas with Efficient Systems
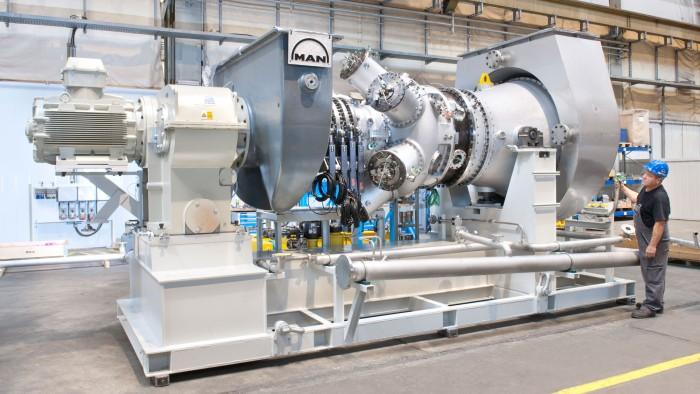
Flaring is a common practice at oil and gas facilities where associated gas generated from oil production and gas processing is burned off through an open flame. This flared gas contains valuable energy resources like methane that simply emit as greenhouse gases into the atmosphere. To recover this wasted gas, flare gas recovery (FGR) systems are increasingly being installed industrywide.
Reasons for Installing Flare Gas Recovery
One of the primary reasons for recovering flare gas is environmental compliance. Flaring emits carbon dioxide and methane, contributing to global warming. Many countries now regulate the volume of gas that can be flared and have set targets to eliminate routine flaring. Recovering flare gas helps facilities meet these emission reduction goals in a cost-effective way.
Another key driver is monetizing an otherwise lost resource. The methane in flare gas has significant energy value that can be captured through FGR systems. The recovered gas can be compressed and fed into the sales gas pipeline to generate revenue. For oil producers, it boosts the overall production value from well operations.
Design and Operation of Typical Flare Gas Recovery Systems
A basic Flare Gas Recovery Systems setup consists of a flare knockout drum, separator, compressor, and pipeline infrastructure to route gas to its end use. Flare headers deliver the flare gas stream to the knockout drum where liquid removal occurs. The gas exits to a separator that further removes any entrained liquids/hydrocarbons.
The dry gas is then fed to a compressed gas system. Reciprocating compressors or centrifugal/screw compressors raise the pressure for pipeline tie-in. Multi-stage compression is often needed to boost low-pressure gas to sales line specifications. Instrumentation and controls automate operations.
Recovered gas quality must meet pipeline standards for heating value, water dew point, and other parameters. Additional treatment like dehydration may be required before transportation. The size and design complexity varies depending on oilfield conditions and gas flowrates/composition.
Challenges in Flare Gas Recovery Projects
While the concept is straightforward, implementing FGR faces multiple challenges. Flare streams contain impurities and toxic substances that impact equipment selection and design. Variable and intermittent flow characteristics make sizing compression difficult. Maintaining reliability with low-pressure feed also poses issues.
Undertaking a flare recovery project requires detailed field characterization. Gathering accurate composition and flow data is crucial for techno-commercial feasibility. Offtake gas quality norms and available pipeline infrastructure need assessment. Capital costs can be high for remote locations with minimal existing facilities.
Operator experience is gaining via improving flare measurement methods, developing robust compressors, and employing advanced automation/controls. Standards are evolving on issues like venting allowances during startup/shutdown. With the technology maturing, more marginal streams will become technically and economically viable to capture.
Ongoing Enhancements in System Designs
Equipment manufacturers continually enhance flare gas recovery systems to withstand variable flows and contaminants. Materials selection focuses on corrosion resistance. Compressors feature modular design and can run on variable speeds for turndown flexibility.
Digital technologies enable remote monitoring of performance parameters. Predictive analytics applied to composition data aids in optimizing operations like maintenance scheduling. Integrating flare header VRUs (vapor recovery units) recovers valuable liquids as well.
Some innovations extract natural gas liquids (NGLs) from the flare stream using hydrocarbon phase separators and boost recovery value. Use of mobile compression packages makes FGR applicable to temporary/portable facilities. Evolving unit designs maximize uptime through automated fault detection.
As concerns over gas flaring intensify and the business case for flare gas recovery strengthens, more operators are installing dedicated FGR facilities globally. Ongoing R&D smoothens technology deployment, especially for low-flow situations. With environmental regulations tightening, flare gas that was once wasted will increasingly get reinjected or fed into sales pipelines through continuous system enhancements.
Get more insights on Flare Gas Recovery Systems
About Author:
Money Singh is a seasoned content writer with over four years of experience in the market research sector. Her expertise spans various industries, including food and beverages, biotechnology, chemical and materials, defense and aerospace, consumer goods, etc. (https://www.linkedin.com/in/money-singh-590844163)
- Art
- Causes
- Crafts
- Dance
- Drinks
- Film
- Fitness
- Food
- Spiele
- Gardening
- Health
- Home
- Literature
- Music
- Networking
- Other
- Party
- Religion
- Shopping
- Sports
- Theater
- Wellness
