Centrifugal Pumps: How They Work and Their Main Components
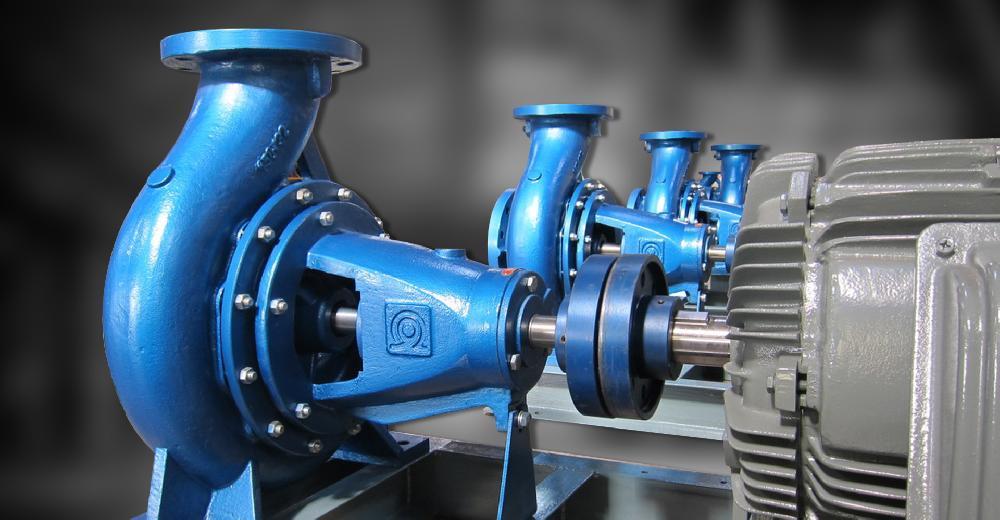
Working Principle of Centrifugal Pumps
Centrifugal pumps work on the principle of centrifugal force. When a fluid enters the eye of an impeller spinning at high speed, it is thrown outward due to the centrifugal force generated. The fluid enters the suction (eye) of the impeller in the axial direction and exits radially from the impeller due to centrifugal force. As the fluid leaves the impeller, it enters the diffuser vanes where pressure is increased. This increase in pressure is caused by the conversion of kinetic energy of the fluid into pressure energy. Thus, the primary function of a centrifugal pump is to increase the pressure energy of the fluid by utilizing the energy imparted by the prime mover.
Main Components of a Centrifugal Pump
Casing: The casing houses the main components like the impeller and shaft seal. It is the outer boundary of the pump through which the fluid enters and exits. Different types of casing designs are used based on Centrifugal Pump applications.
Impeller: The impeller is the most important and critical component of a centrifugal pump. It consists of a hub with radial vanes and generates centrifugal force by its high-speed rotation inside the casing. Different impeller designs are used based on head, flow rate and solids handling requirements.
Shaft: The shaft transmits the rotational power from the driver to the impeller. It is usually made of high-strength alloy steel and supported by bearings. Shaft sleeves are sometimes used to isolate the impeller from radial loads and shaft deflection.
Bearings: Bearings support the shaft and allow smooth rotation of the impeller inside the pump casing. Common bearing types used are journal bearings, anti-friction bearings and thrust bearings. Bearing housings provide boundary lubrication and cooling to the bearings.
Seal: Mechanical seals or packings are used to prevent leakage of fluid along the shaft. Various types of mechanical seals like single seals, double seals, cartridge seals are used based on fluid and application requirements.
Suction and Discharge Piping: Suction piping brings fluid into the pump suction nozzle and discharge piping carries the pressurized fluid from the pump discharge flange to the system. Proper sizing, material selection and supports are important for smooth flow.
Drive Unit: Electric motors, diesel or gas engines are commonly used as drive units for centrifugal pumps. Direct drive coupling or V-belts connect the driver to the pump shaft.
Different Types of Centrifugal Pumps
Centrifugal pumps are classified mainly based on impeller design and casing configuration. Here are some common types:
Radial Flow Pumps: These have straight-through impellers with vanes perpendicular to shaft. Used for low to moderate pressure applications up to 60m head.
Axial Flow Pumps: Impeller vanes are parallel to shaft. Used where high flows at low heads are required. Applications include axial drainage pumps and axial booster pumps.
Mixed Flow Pumps: Intermediate design with vanes angled 45 degrees. Can handle slightly higher pressures than radial but lower than axial pumps. Common in filtration and irrigation.
Multi-Stage Pumps: Consists of several impellers separately housed to incrementally boost pressure. Required for very high pressure services above 400m head. Used in boiler feed, pressure boosting etc.
Vertical In-Line Pumps: Shaft and impeller positioned vertically. Impellers arranged one above the other. Self-priming capability. Common in wastewater, sewage, dewatering applications.
Submersible Pumps: Hermetically sealed wet-pit pump with motor mounted below at bottom of impeller. Frequently used for groundwater drainage, sewage transfer, fountains etc.
Axial-Flow Sump Pumps: Non-clog pumps able to handle solids in wastewater and sewage handling. Solids pass straight through without damaging impeller due to large clearances.
Centrifugal Pumps Applications
Given their robust and trouble-free operation, centrifugal pumps find widespread application across industries and facilities. Here are some common uses:
- Chilled/Hot Water Circulation Systems: Circulate water in HVAC systems of buildings, industries etc.
- Boiler Feedwater and Condensate Return: Supply feedwater to boilers and return condensate in thermal power plants.
- Irrigation Systems: Lift water from open wells or tanks for irrigation of crops.
- Sewage and Wastewater Transfer: Transport sewage in municipal networks and wastewater in effluent treatment plants.
- Cooling Water Systems: Circulate cooling water for cooling towers, heat exchangers in process industries.
- Fire Protection Systems: Automatically pressurize underground piping in case of fire for sprinklers.
- Marine Transfer Pumps: Used onboard ships and vessels to transfer fuel, ballast, bilge and firefighting fluids.
- Pulp and Paper Mills: Used at various stages to move slurries and process liquids.
With their wide range of designs and models available, centrifugal pumps will continue to be indispensable pieces of equipment in industrial and domestic applications requiring fluid transfer and pressure boosting. Their simple and robust operation ensures reliable performance even in toughest conditions.
Pick the language that you prefer
About Author:
Priya Pandey is a dynamic and passionate editor with over three years of expertise in content editing and proofreading. Holding a bachelor's degree in biotechnology, Priya has a knack for making the content engaging. Her diverse portfolio includes editing documents across different industries, including food and beverages, information and technology, healthcare, chemical and materials, etc. Priya's meticulous attention to detail and commitment to excellence make her an invaluable asset in the world of content creation and refinement.
(LinkedIn- https://www.linkedin.com/in/priya-pandey-8417a8173/)
Nach Verein filtern
Read More
The Spain Eyewear Market Size is Anticipated to Reach USD 8.97 Billion by 2033, growing at a CAGR of 8.17% from 2023 to 2033. The Spain Eyewear in Spain includes glasses, sunglasses, and goggles, serving both functional and fashion purposes. Known for creativity and innovation, Spanish eyewear reflects heritage and modern style. It protects from environmental elements, enhances...
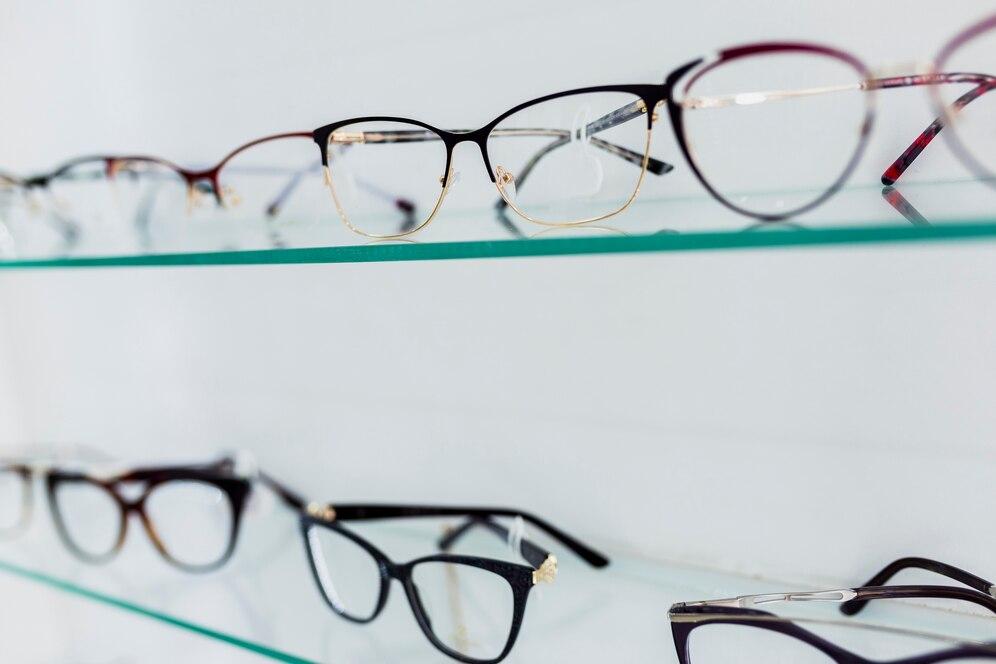
The report presents a thorough analysis of the Middle East & Africa Smart Water Management Market, including market size, share, growth, market expansion, technical advancements, trends, cost structure, revenue, statistics, and detailed market data. This market study analyzes overall market growth prospects on regional level. It also reveals comprehensive competitive marketplace of the...
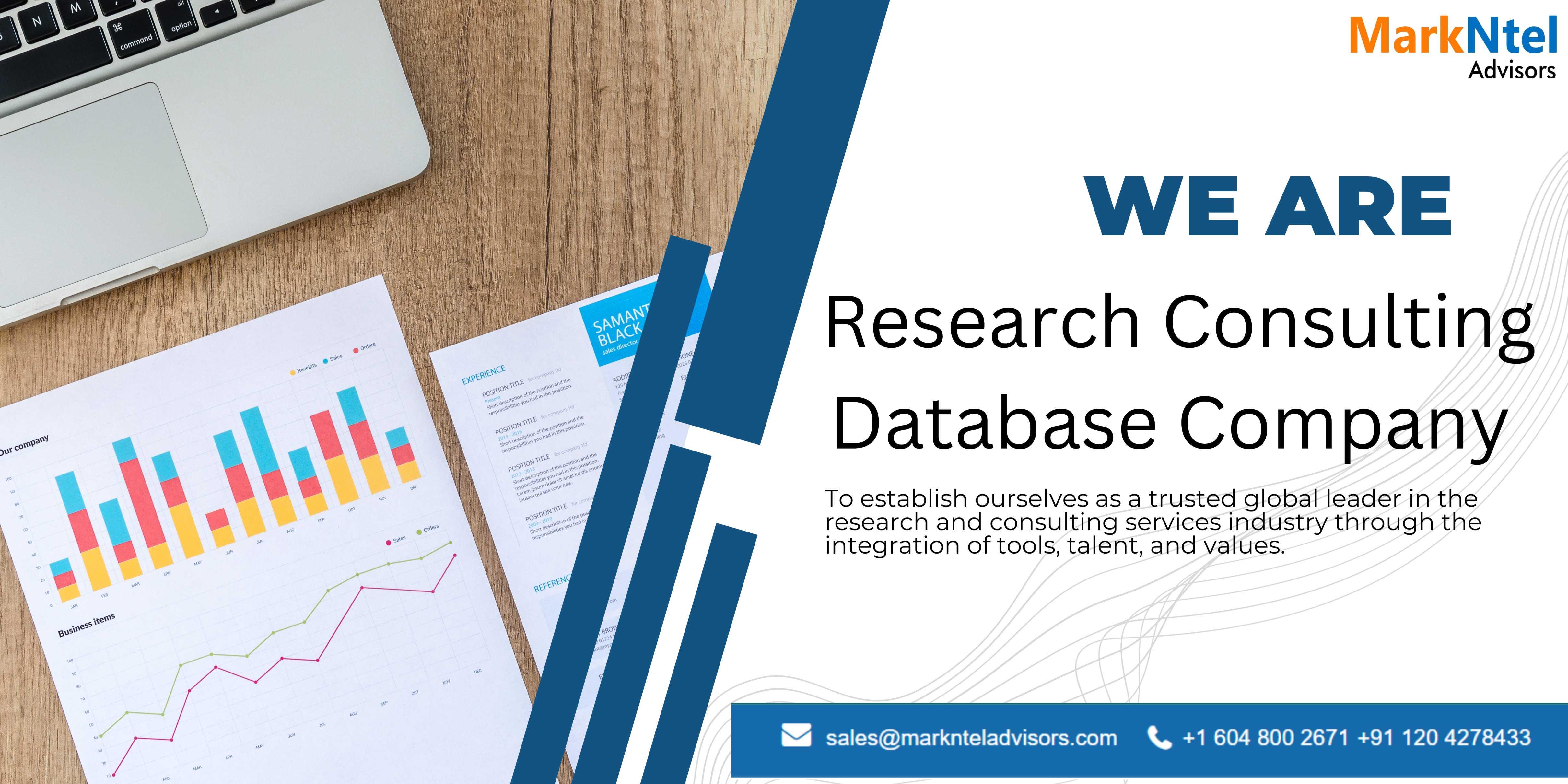